How SINO makes bronze/ brass sculptures?
1. Designing.
Our design team will design 2-3 drafts for comparison and selection according to the customer's design requirements. The design carrier needs to be selected according to the shape of the sculpture. If it is a sculpture of a character, an animal, or an irregular, complicated texture, or the shape is too small, we will make a clay model. If the shape is regular, it can be done directly using computer 3D modeling technology.
Alternatively, if the customer has a design, if it is a small draft, we will generally perform a 1: 1 scale-up process, and then combine the production process and internal structure requirements to properly optimize the model without changing the external shape of the sculpture.
Sketches for design stage
3D drawing design
2. Modeling
Clay modeling and 3D modeling are only the first steps in making a model. After obtaining the clay model confirmed by the customer, the FRP model will be converted afterward to facilitate the transportation and storage of the model. In the foundry, silicone, and wax molds are produced. The 3D model will directly use 3D printing or engraving technology to produce a more accurate model quickly and directly. Then, a silicone mold and a wax mold are followed.
Put the prepared wax mold into the soaking tank, to make it wet, and take it out and wrap it with quartz sand, then hang it to dry for the next step use.
3D modeling
3. Casting
The wax mold coated with quartz sand will become hard after drying, putting it in the furnace and heating it, so that the wax inside will melt out from the reserved holes. Slowly pour the molten copper and bronze water from the reserved injection opening into the mold. After being left to cool, the quartz sand is knocked out, and then the sandblasting treatment is performed to obtain a copper bronze casting product.
Clay sculpt for detailed texture surface
Duplicated into FRP model
Silicon mold reproduction
Make wax models
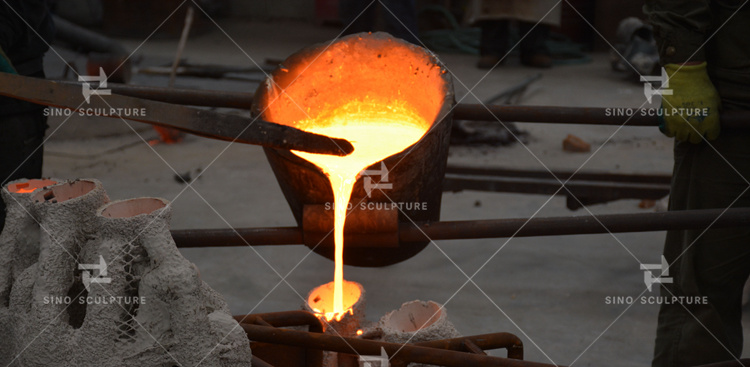
Lost wax casting
4. Welding
For small sculptures, we can cast them all at one time, which is simpler. However, large-scale bronze sculptures, need to be divided into small pieces for block casting. Welding each single cast copper plate after casting to form a complete large-scale copper sculpture.
Small size bronze casting process
Big size bronze casting process
5. Grinding & Polishing
After sandblasting, the surface is still uneven or smooth, which requires grinding and polishing to make the surface of the copper bronze sculpture smooth. This process requires a special polishing master to complete the polishing process of the sculptural surface using various sizes of polishing equipment. This process plays a very important role in the later molding of the sculpture.
Grinding and polishing the surface and weld seam
6. Finish
To make the sculpture look more beautiful, to reduce the corrosion damage to the sculpture by harmful substances such as acidic air and moisture, and to prolong the service life of the sculpture, special treatment is usually applied to the bronze outer surface. The most commonly used bronze sculpture surface treatment methods are patina, painting, gold leaf, and electroplating. We do not recommend mirror polishing, because the copper-bronze material will be oxidized very quickly if it is directly exposed to the air, and the mirror effect will be destroyed in a short time. The post-maintenance cycle will be shorter and the cost will be higher.
After the surface treatment, a bronze sculpture is completed. The whole process seems simple, but it is also very difficult to grasp the key steps, such as how to cast more perfectly when pouring, without generating bubbles, or how to better repair small sand holes when welding.
Bronze cast statue with gold leaf gilding
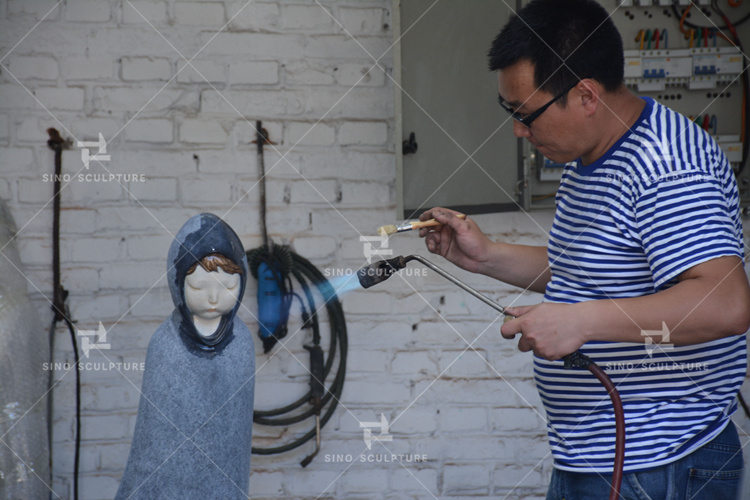
The process of patination